What is GRP?
GRP stands for Glass Reinforced Plastic (or Polymer). It’s also known as FRP (Fibre Reinforced Plastic) or Fibreglass. It is a blend of recycled plastic and recycled glass bonded together with a tough, waterproof resin which is then moulded or pultruded into the required shape – whether that’s a panel of open mesh or grating to use as flooring or fencing, or long, smooth profiles used to build the framework of a structure. An extra layer, embedded with sharp quartz grit, is often added to the top to create a slip-resistant surface that remains effective in wet, icy or even oily conditions.
Originally developed for the boating industry as a lightweight, tough, waterproof alternative to wooden hulls, it has become common-place within other industries and can now be found in buildings, factories, utility plants, power stations, railway stations, marinas and docks across the globe.
As more and more industries explore the benefits of using GRP instead of steel, different types have been developed to cope with some of the world’s most inhospitable environments. They are made by using different qualities of resin to bond with the glass and plastic.
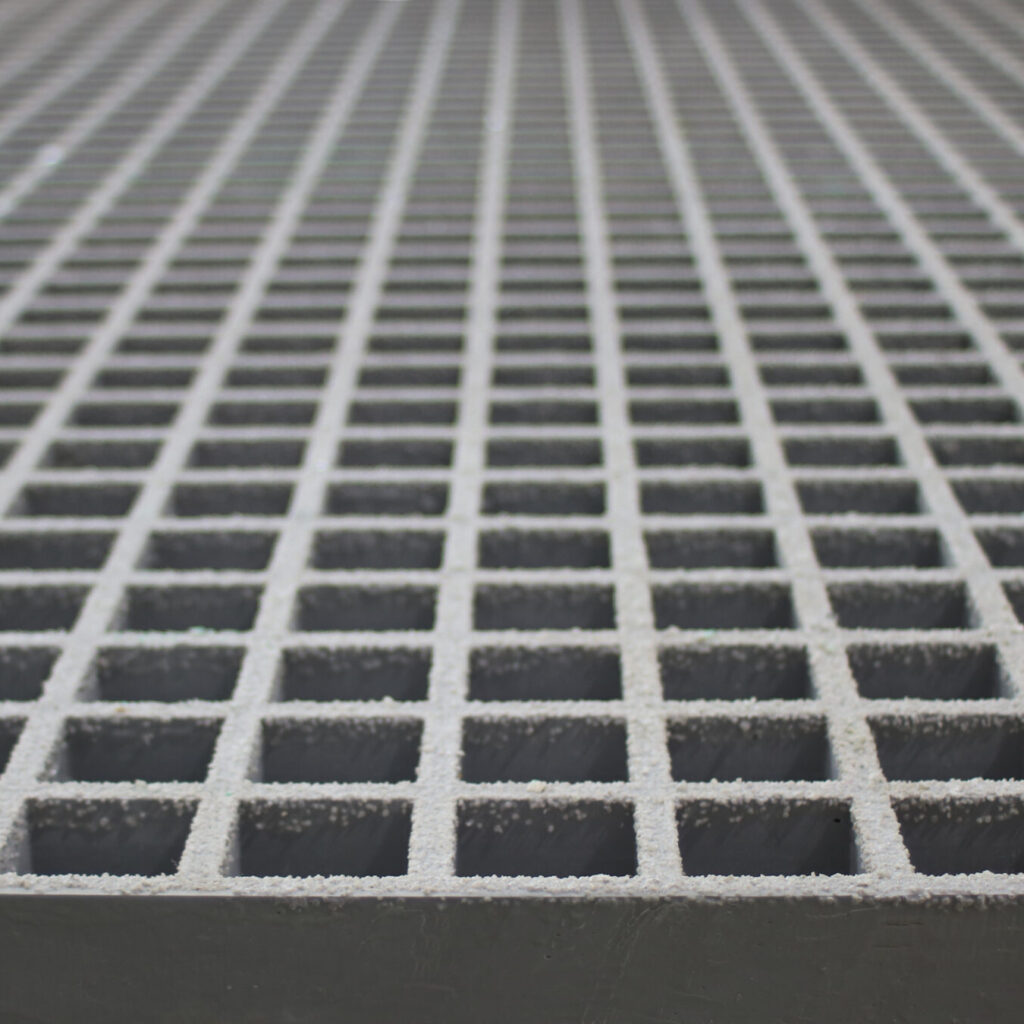
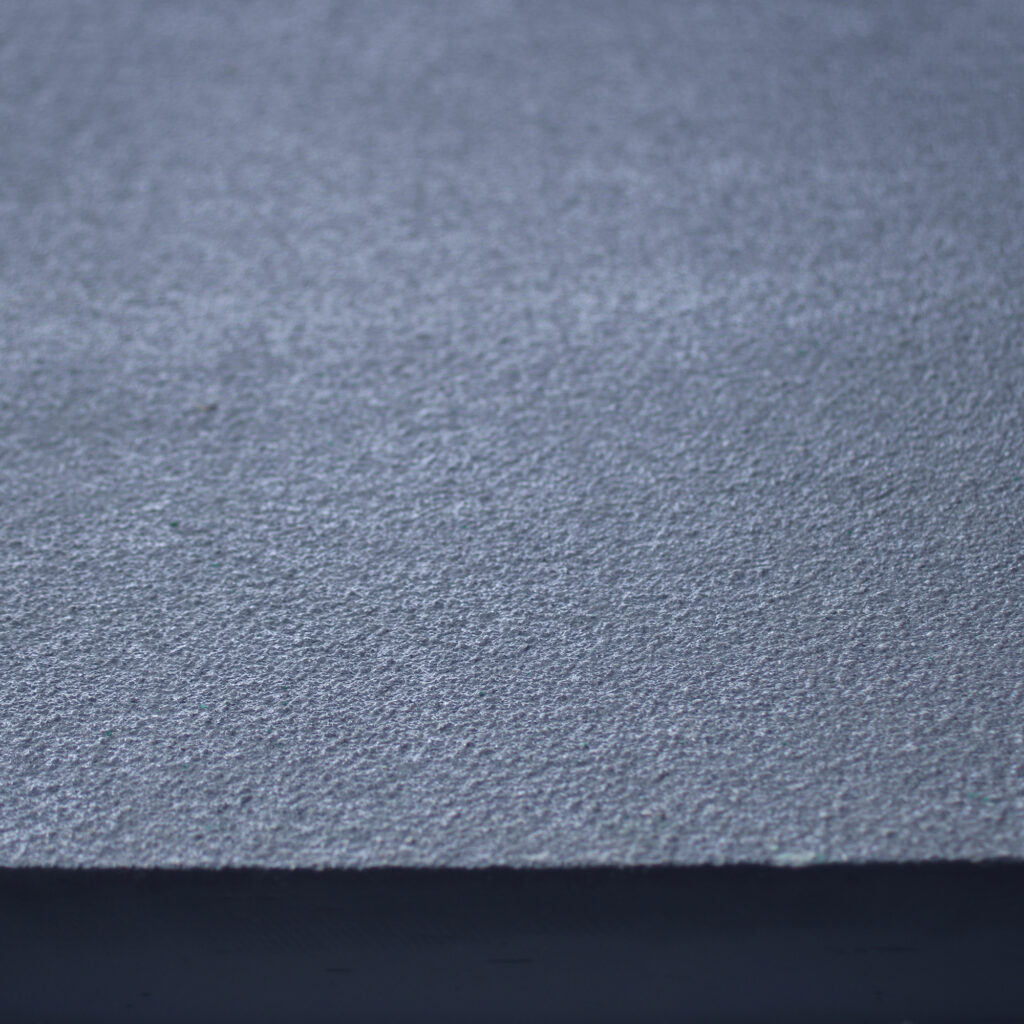
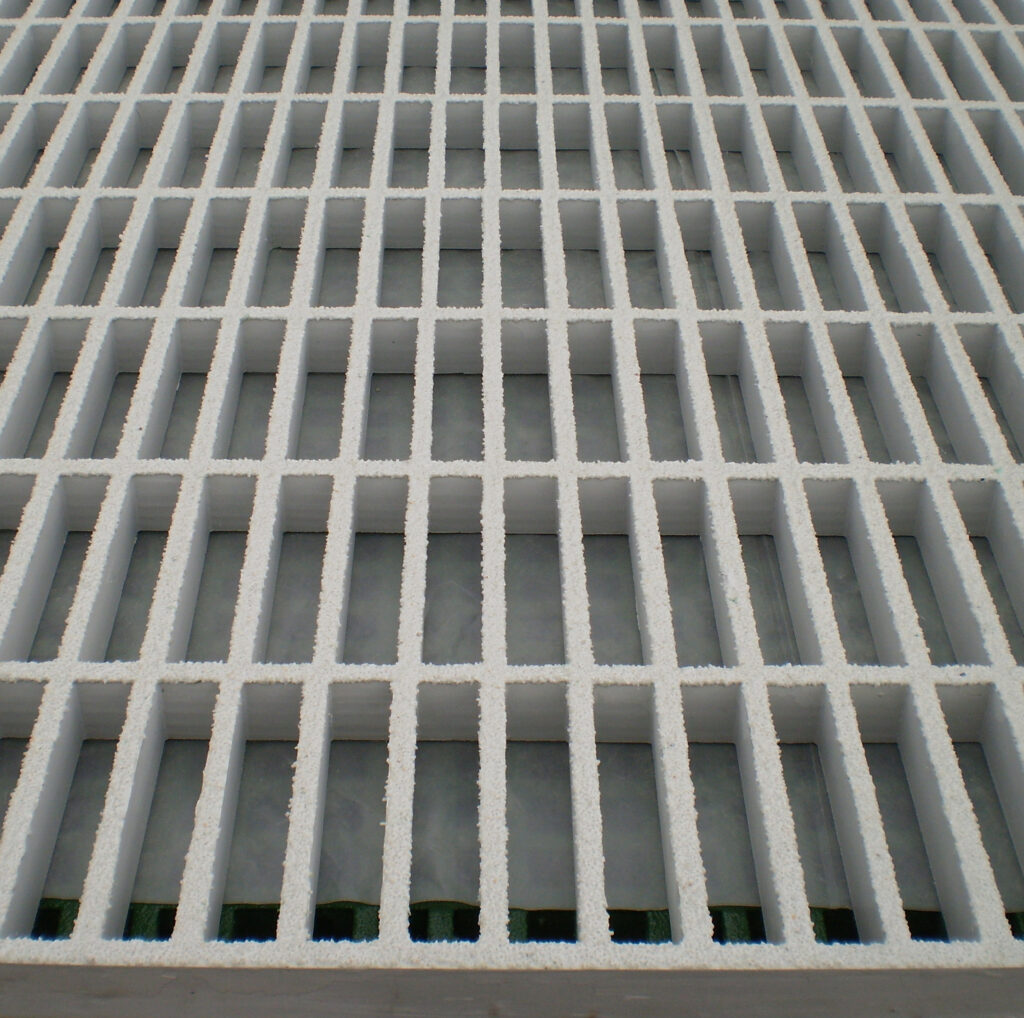
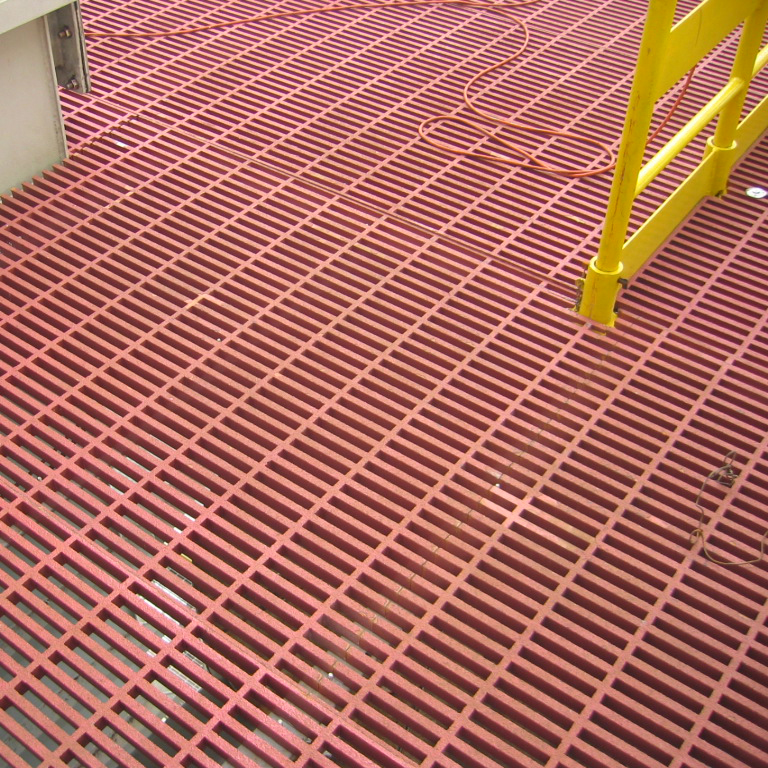
Orthophthalic (Ortho)
Ortho resins are based on orthophthalic acids and are a good, general purpose and inexpensive choice. They are most commonly used for applications that aren’t subject to high temperatures or highly corrosive environments
Isophthalic (Iso)
GRP made with Iso resins are better suited to corrosive environments and can cope with higher temperatures. They have greater mechanical properties too which means they are the ones most commonly used when building structures. For this reason, they generally cost more to produce than the Ortho versions.
Vinyl Ester
Much denser than Ortho or Iso resins, Vinyl Ester GRP products are more able to absorb impact without damage and are often used to reinforce structures made from Iso or Ortho resin.
Phenolic
Grating made from Phenolic GRP is the latest and most strongest version to date and can be found in the most hostile of environments including oil refineries, oil platforms, underground mining, railways and in shipping. It has the maximum fire resistance and emits little smoke or toxic fumes when burning – critical in enclosed spaces. Its reinforced structure can take exceptional loads – useful where large, uninterrupted spans need to be bridged.
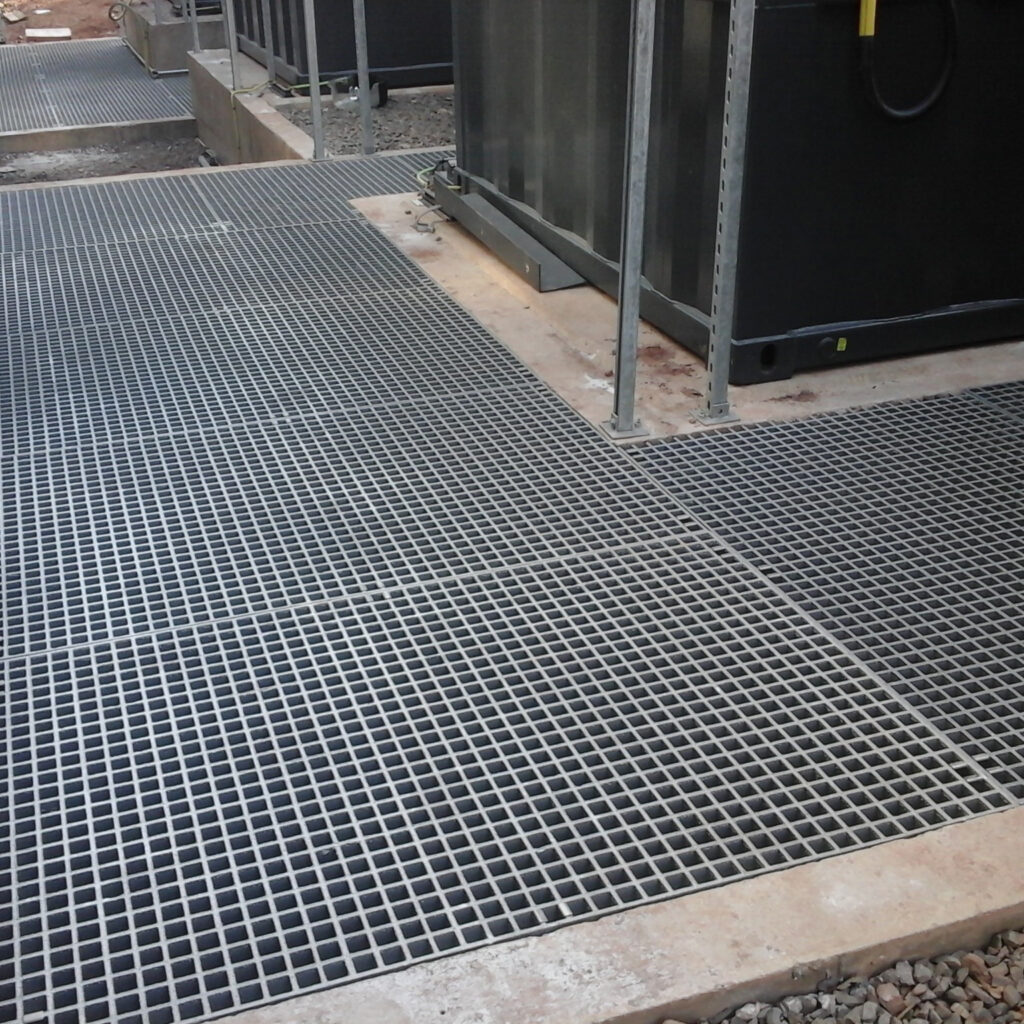
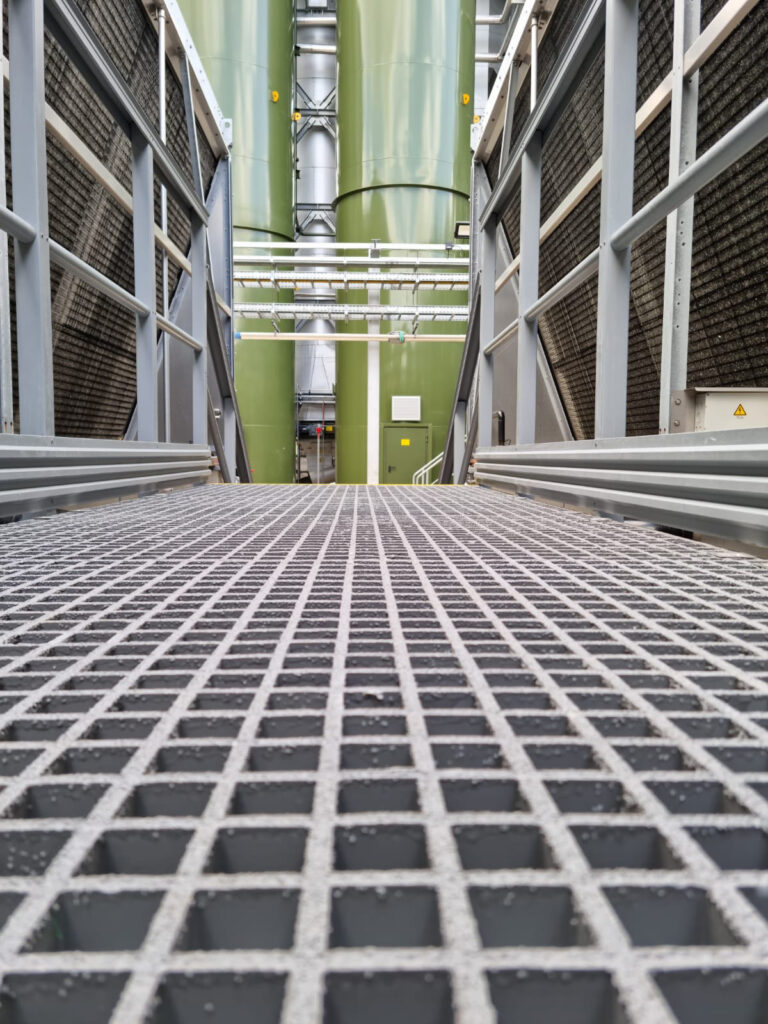
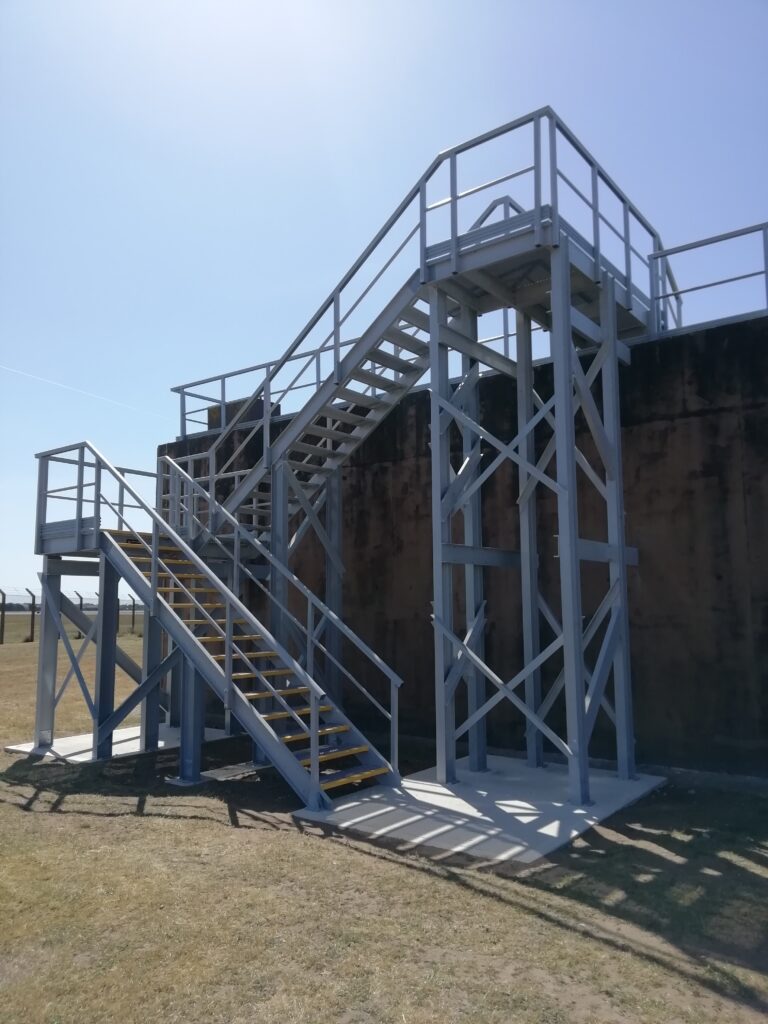
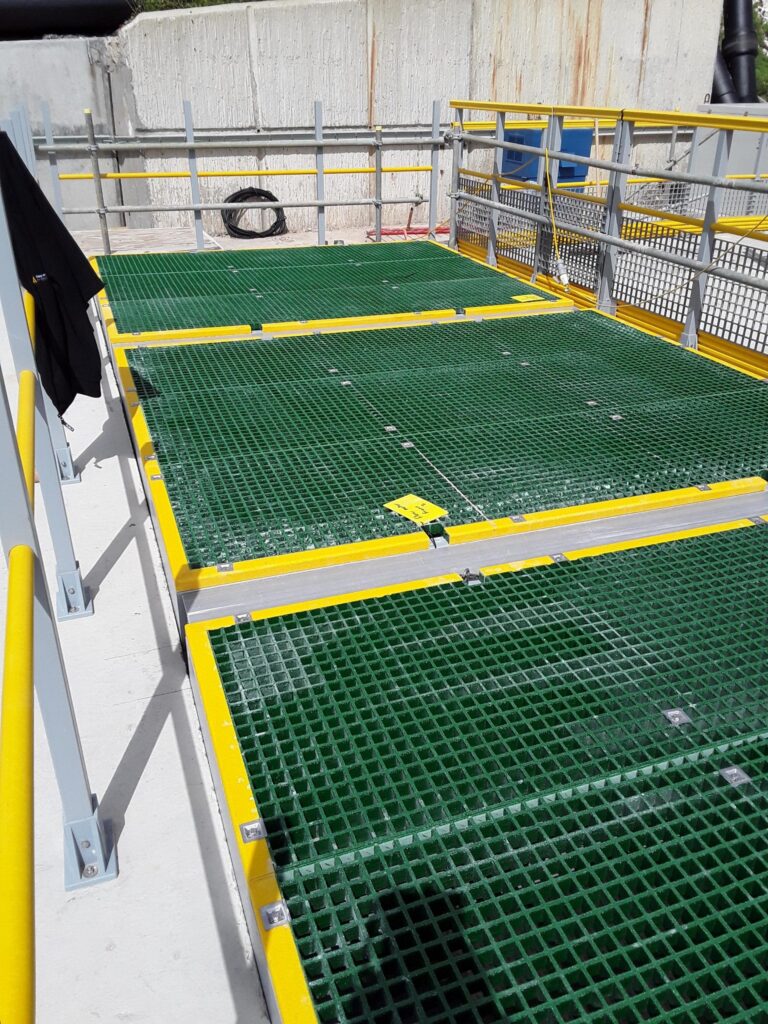
Why Choose GRP?
More and more specifiers and project managers are switching from steel and timber to GRP alternatives; here are some of the reasons why:
- It won’t go rusty
Steel is at risk from any moisture – whether that’s water vapour, rainwater, river water, sea water or water from drainage, sewage or sluicing. Which means that, even on indoor applications, if you want to clean it you run the risk of starting corrosion. GRP does not rust - It’s chemical-resistant
GRP grate flooring is not only impervious to water, it’s resistant to hundreds of other chemicals that will damage metal over time - It lasts longer
Like all plastic-based products, the GRP lifetime is measured in terms of decades – up to 50 years in some applications – so, once it’s installed, it won’t need replacing anytime soon. In fact, we’re so confident in its longevity that we offer a 15-year warranty on all our GRP products - It’s low maintenance
It never needs painting or re-coating. The colour is part of the material it’s made from, so it won’t wear off or chip - It’s UV-stable
The colour won’t fade in sunlight (or any other light); if you’re using a bright colour to warn people of a hazard, it will be just as noticeable ten years after installation as the day it was new - It’s lightweight
A four metre panel is still a two-man lift but it’s up to half the weight of the steel equivalents, which makes GRP much easier to move. Travelling from site to site, vehicles will use less fuel – within a site it can be moved manually or by forklift – no cranes required. This represents a huge cost saving in installation alone - It’s fire resistant
All our GRP grate flooring contains a fire-resistant additive which complies with Euro Class 1 and ISO11952-2. Performance in tests matched ASTM E84 class 1 and BS476 part7 class 2 flame spread to give a 30-minute burn time - It’s slip-resistant
Our QuartzGrip fibreglass grating has an integral layer of quartz grit embedded in the top, offering a superb, non-slip finish effective in wet, icy and even oily conditions - It’s non-conductive
You won’t get an electric shock from standing on a GRP floor. However, if a static spark could pose a threat (because of flammable gas or fumes) there is a conductive alternative that can be earthed - It’s easy to cut
All that’s needed is a heavy-duty saw. There are no sparks created when cutting GRP panels or profiles, so there is no fire risk and no Hot Works permits are required - It doesn’t conduct heat
GRP feels warmer than steel as it doesn’t absorb body heat, so it’s more comfortable to work around - It’s quieter
Running up or down a steel staircase is a noisy; GRP Walkways and Staircases don’t resonate in the same way making for a less disruptive working environment - It comes in a range of colours
Standard colours are green, grey, beige and yellow but it can actually be produced in any RAL colour to suit your branding
If you’d like to know more take a look at our range here. All our Isophthalic GRP products are stocked for immediate UK delivery but we can deliver to anywhere on the planet – including mid-ocean. If you are looking for one of the more specialist varieties, please get in touch with us.